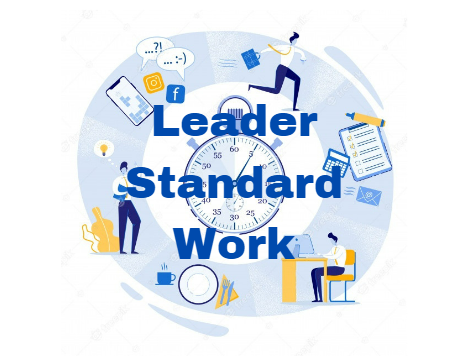
Leader Standard Work – Feb 9th (FULL, join waitlist)
Leader Standard Work: Creating your new leadership routine (online class) Class Description The February 9th class is full, but the waitlist is growing. Please let Jennifer know if you’re interested in this topic, we will likely hold another class in March. The true purpose of leadership is to empower and develop your employees so they can achieve awesome things. To accomplish this, you need a standard way of working that will allow you to maximize your efficiency and impact while fulfilling your most important duty to your people.As the whirlwind takes over our day, we quickly lose control of our priorities. Once we fall into firefighting mode, our ability to improve and sustain processes and activities becomes secondary. This is where Leader Standard Work (LSW) comes into play. LSW is the…