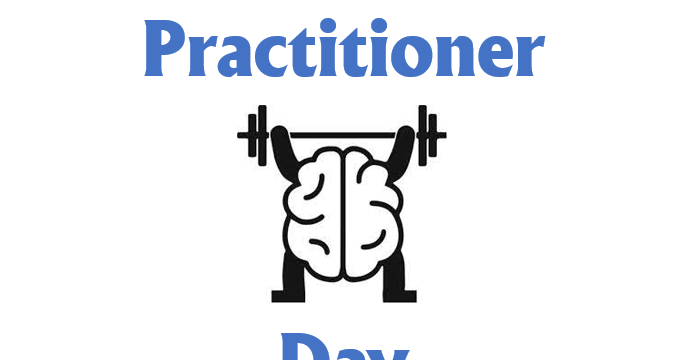
Kata Practitioner Day – March 22nd (Full)
Explore the 4-step Improvement Kata method through practitioners sharing real world examples. What is Toyota Kata? It's two intentional routines - the Improvement Kata, layered with the Coaching Kata. Together, these two routines help individuals become stronger, more confident problem solvers. The purpose of a Kata Practitioner Day is to: Provide a forum to learn from your fellow NWHPEC Kata practitioners, Introduce the Improvement Kata and Coaching Kata to those new to this improvement and skill building approach, and Hear how the Improvement Kata and Coaching Kata is being applied in all aspects of an organization Event Details: Date: Wednesday, March 22, 2023Time: 9am – noonLocation: Smith Gardens (23200 Hubbard Cutoff Rd NE, Aurora, OR)Cost: No charge (we just ask that you aren’t a no-show)Registration: Limited to NWHPEC members. Email…